Can a Compressor Be Repaired?
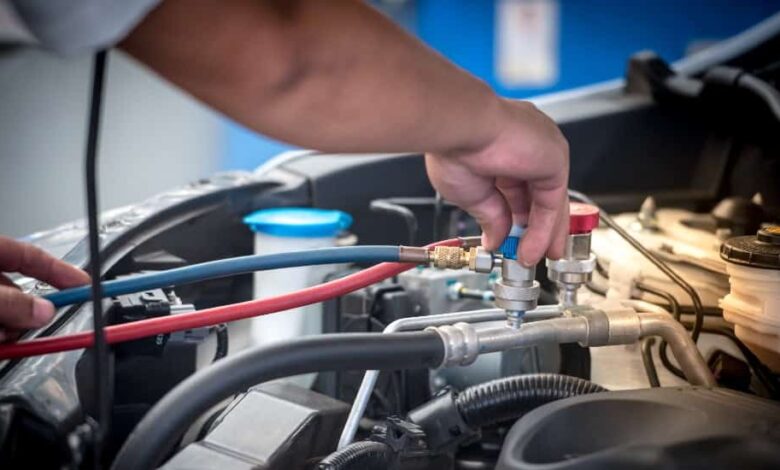
Compressors are crucial components in various mechanical and industrial systems, from refrigeration units to air conditioning systems, pneumatic tools, and more. Given their widespread use, it’s not uncommon for these devices to experience issues that might lead one to ponder: can a compressor be repaired? The short answer is yes, compressors can often be repaired, but the feasibility, cost-effectiveness, and approach depend on the specific type of compressor, the nature of the problem, and the availability of parts and expertise.
Understanding Compressors and Their Functionality
To appreciate the repairability of compressors, it’s essential to understand their basic operation and types. Compressors work by increasing the pressure of a gas by reducing its volume. This principle is used in various applications, including powering air tools, refrigeration cycles, and even in the automotive industry. The main types of compressors include reciprocating (piston) compressors, rotary screw compressors, centrifugal compressors, and scroll compressors, each with distinct mechanisms and applications.
Reciprocating compressors use a piston within a cylinder to compress gas, similar to how an engine’s cylinder works. Rotary screw compressors use two interlocking helical screws to compress the gas. Centrifugal compressors use a rotating impeller to impart velocity to the gas, converting this velocity into pressure. Scroll compressors use two interleaving spiral elements to compress the gas. The complexity and specific mechanics of these types influence how they can be repaired.
Common Compressor Problems
Compressors, like any mechanical device, are prone to various issues. Common problems include:
Electrical failures: These can involve issues with the motor, wiring, or other electrical components. Electrical failures can cause the compressor to stop working or operate inefficiently.
Mechanical failures: These include issues such as worn-out bearings, broken valves, or damaged pistons in reciprocating compressors. Mechanical wear and tear can lead to reduced efficiency or complete failure.
Refrigerant leaks: In refrigeration and air conditioning systems, leaks in the refrigerant lines can lead to a loss of cooling capacity and compressor damage.
Overheating: Compressors can overheat due to various factors, including inadequate ventilation, excessive workload, or internal component failure.
Contamination: Dirt, debris, or moisture can contaminate the internal components of the compressor, leading to operational issues.
Understanding these common problems helps in diagnosing and deciding whether a compressor can be repaired.
Diagnosing Compressor Issues
Effective repair begins with accurate diagnosis. Diagnosing compressor problems typically involves several steps, starting with a visual inspection to check for obvious signs of damage, such as leaks, worn belts, or loose connections. Listening for unusual noises can also provide clues; for example, rattling might indicate loose parts, while a screeching sound could suggest bearing issues.
Advanced diagnostics might involve using tools like multimeters to check electrical components, pressure gauges to measure output pressure, and thermal imaging cameras to detect overheating components. In more sophisticated setups, diagnostic software can be used to monitor compressor performance and identify anomalies.
Once the problem is identified, the feasibility of repair can be assessed. Some issues, like minor leaks or electrical component failures, can often be repaired relatively easily. Others, such as major mechanical failures, might require significant parts replacement or even complete overhaul.
Repair vs. Replacement
Deciding whether to repair or replace a compressor depends on several factors, including the age and condition of the compressor, the cost of repair compared to replacement, and the availability of parts. For newer compressors, especially those still under warranty, repair is often the preferred option. However, for older units, especially those nearing the end of their expected lifespan, replacement might be more cost-effective in the long run.
Cost is a significant factor. Simple repairs, such as replacing a capacitor or fixing a small leak, are usually inexpensive. However, major repairs, such as replacing a motor or a set of pistons, can be costly. If the cost of repair approaches or exceeds the cost of a new compressor, replacement is generally the better option.
Availability of parts is another crucial consideration. For older compressors or those from less common manufacturers, finding replacement parts can be challenging and expensive. In some cases, custom parts might be required, further increasing the cost and complexity of repair.
The Repair Process
The process of repairing a compressor typically involves several steps. Once the problem has been diagnosed and a decision has been made to proceed with repair, the next step is disassembly. This involves carefully taking apart the compressor to access the faulty components. It’s essential to follow the manufacturer’s guidelines and use the appropriate tools to avoid causing further damage.
After disassembly, the faulty parts are replaced or repaired. This might involve tasks such as soldering electrical connections, replacing worn bearings, or resealing joints. In some cases, it might also involve machining new parts or reconditioning existing ones.
Once the repairs are complete, the compressor is reassembled and tested. Testing involves running the compressor under various conditions to ensure it operates correctly and efficiently. Any issues identified during testing need to be addressed before the compressor can be put back into service.
Preventive Maintenance
Preventive maintenance is crucial in extending the lifespan of compressors and reducing the likelihood of major repairs. Regular maintenance tasks include checking and replacing filters, lubricating moving parts, inspecting belts and hoses, and ensuring proper ventilation. For refrigeration and air conditioning compressors, checking for refrigerant leaks and ensuring the refrigerant levels are correct is also important.
Regular maintenance not only helps in preventing major issues but also improves the efficiency and reliability of the compressor. A well-maintained compressor operates more efficiently, consumes less energy, and provides more consistent performance.
Specialized Repair Services
For complex issues or large industrial compressors, specialized repair services might be necessary. These services often have the expertise, tools, and facilities to handle major repairs and overhauls. They can also provide valuable advice on whether repair or replacement is the better option and offer warranties on their work.
Choosing a reputable repair service is important. Look for companies with experience in repairing the specific type of compressor in question, and check for reviews or testimonials from previous clients. Reputable services often provide detailed diagnostics and transparent pricing, ensuring that you understand the scope and cost of the repair before work begins.
Advances in Compressor Technology and Repair
Advances in technology are also impacting the repair and maintenance of compressors. Modern compressors often come equipped with sensors and diagnostic tools that can provide real-time data on their operation. This data can be used to predict and prevent failures, improving reliability and reducing downtime.
In addition, new materials and manufacturing techniques are leading to more durable and efficient compressors. For example, the use of advanced ceramics in bearings can reduce wear and increase lifespan, while improvements in seal technology can reduce leaks and improve efficiency.
These advances are making compressors more reliable and easier to maintain. However, they also mean that repair technicians need to stay up-to-date with the latest developments and have access to the latest tools and equipment.
Environmental Considerations
Environmental considerations are becoming increasingly important in the repair and maintenance of compressors. For example, properly handling and disposing of refrigerants is crucial in preventing environmental damage. Many older refrigerants are harmful to the ozone layer, and newer, more environmentally friendly alternatives are being used.
In addition, improving the efficiency of compressors through regular maintenance and timely repairs can reduce energy consumption and greenhouse gas emissions. Efficient compressors use less energy, which not only reduces operating costs but also has a positive impact on the environment.
Conclusion
In conclusion, compressors can indeed be repaired, and doing so is often a cost-effective and environmentally friendly option. The feasibility and cost of repair depend on various factors, including the type of compressor, the nature of the problem, and the availability of parts and expertise. Accurate diagnosis is the first step in the repair process, followed by careful disassembly, repair or replacement of faulty components, and thorough testing.
Preventive maintenance plays a crucial role in extending the lifespan of compressors and reducing the likelihood of major repairs. Advances in technology are making compressors more reliable and easier to maintain, but they also require repair technicians to stay up-to-date with the latest developments.
Specialized repair services can handle complex issues and provide valuable advice on repair versus replacement. Environmental considerations are increasingly important, with proper handling of refrigerants and improving efficiency being key factors.
By understanding the principles of compressor operation, common issues, and the repair process, you can make informed decisions about the maintenance and repair of these essential devices. Whether it’s a small air compressor for home use or a large industrial unit, timely and effective repair can keep your systems running smoothly and efficiently.