How Does It Work? The Science Behind Strain Gauge Measurements
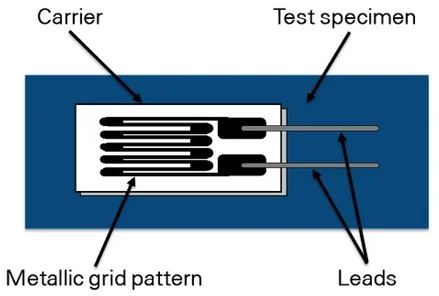
Have you ever wondered how engineers measure the invisible forces acting on structures? The answer lies in a tiny but mighty sensor called a strain gauge. These unsung heroes play a crucial role in ensuring the safety and integrity of everything from towering skyscrapers to delicate airplane wings. But how exactly do these miniature marvels translate physical strain into measurable data? Let’s delve into the fascinating science behind strain gauge measurements.
Understanding Strain: The Essence of Measurement
At its core, a strain gauge measures strain, which is the deformation or change in the shape of an object when subjected to external forces. This deformation can be stretching (tension) or squeezing (compression). Imagine stretching a rubber band; the longer it gets, the greater the strain. Strain is a unitless quantity, expressed as a ratio of the change in length (ΔL) to the original length (L) of the object. Mathematically, strain (ε) is represented as:
ε = ΔL / L
The Electrical Connection: From Strain to Resistance
A typical strain gauge consists of a thin metallic foil pattern bonded to a flexible backing. This foil acts as a conductor, and its electrical resistance is directly proportional to its length. When the object experiences strain, the foil deforms along with it. If the object stretches (positive strain), the foil lengthens, causing its resistance to increase. Conversely, compression (negative strain) shortens the foil, leading to a decrease in resistance. This change in resistance, though minute, forms the basis for strain measurement.
The Power of the Wheatstone Bridge: Unveiling the Tiny Signal
The raw resistance change from the strain gauge is typically very small. To amplify and measure this delicate signal, engineers employ a clever circuit called a Wheatstone bridge. This bridge comprises four resistors arranged in a diamond configuration. Two of these resistors are the strain gauge itself, wired in one arm of the bridge. The other two arms contain precisely calibrated resistors with a fixed resistance value.
When no external force acts on the object, the bridge is balanced, meaning the voltage across its output is zero. However, when strain is applied, the resistance of the strain gauge changes, disrupting the balance. This imbalance creates a small voltage at the bridge output, which is directly proportional to the strain experienced by the object. The greater the strain, the larger the output voltage.
The Gauge Factor: Quantifying the Relationship
The relationship between the measured resistance change and the actual strain is not a simple one-to-one correspondence. It’s here that the concept of the gauge factor (GF) comes into play. The gauge factor is a material property that defines the sensitivity of a particular strain gauge. It’s the ratio of the relative change in resistance (ΔR/R) to the applied strain (ε). Mathematically:
ΔR/R = GF * ε
By knowing the gauge factor of the chosen strain gauge and measuring the bridge output voltage, engineers can calculate the actual strain experienced by the object.
Beyond the Basics: Advanced Techniques and Considerations
Strain gauge technology offers a diverse range of configurations and applications. Different types of strain gauges cater to specific needs, such as measuring shear stress or high temperatures. Specialized techniques like rosette gauges with multiple gauges arranged in specific patterns allow for measuring strain in multiple directions.
However, strain gauge measurements also come with their own set of challenges. Temperature fluctuations can affect the resistance of the gauge itself, leading to errors. Careful selection of materials and temperature compensation techniques are crucial for accurate measurements. Additionally, proper strain gauge installation and bonding techniques are essential to ensure reliable data.
FOR MORE INFORMATION CLICK HERE : staycation deals uae
The Invisible Force Detectors: Impact Across Industries
Strain gauges are the workhorses behind countless innovations across various industries. They play a vital role in structural health monitoring of bridges, buildings, and aircraft. They ensure the safety and performance of automobiles by monitoring stress on critical components like suspension systems. In the medical field, strain gauges find applications in prosthetics and implants, helping doctors understand how these devices interact with the body.
Conclusion: The Unsung Heroes of Engineering
Strain gauges, though small in size, play a giant role in the world of engineering. By harnessing the science of strain and resistance, these invaluable sensors provide engineers with the data they need to build safer, stronger, and more efficient structures. As technology continues to evolve, strain gauges will undoubtedly remain at the forefront of ensuring the integrity and resilience of the world around us.