How CNC Turning Stands Out from Traditional Methods
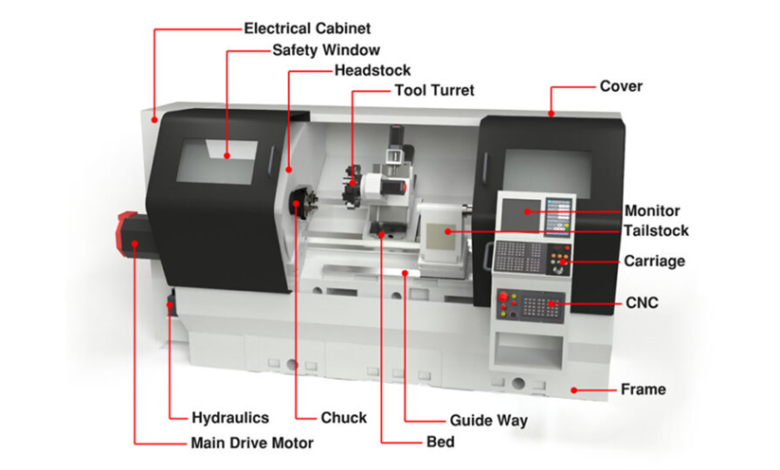
CNC turning is a CNC machining process in which a cutting tool (usually a non-rotating part of a lathe or turning center) removes material from a rotationally rigid material. It can produce different shapes and sizes depending on the turning operation used.
This article will give you an overview of what a lathe or turning center is, what shapes can be produced through this process, and how it compares to CNC milling.
What is CNC Turning?
CNC turning is a precise and automated manufacturing process used to create cylindrical parts. Utilizing computer numerical control (CNC) technology, this process allows for high levels of accuracy and repeatability.
CNC turning is a machining process in which a cutting tool, typically a non-rotary tool bit, moves linearly while the workpiece rotates.
The movement of the cutting tool is controlled by computer programming, which ensures precise dimensions and shapes. This method is ideal for producing symmetrical objects such as shafts, bolts, and bushings.
The main components of a CNC turning machine include the spindle, which holds and rotates the workpiece, and the turret, which houses the cutting tools.
The machine also comprises a bed, where the workpiece is mounted, and a control panel for inputting the CNC program. Key machinery elements:
- Spindle: Rotates the workpiece at high speeds.
- Turret: Holds multiple cutting tools that can be indexed and changed automatically.
- Chuck: Clamps the workpiece securely.
- Tailstock: Provides additional support for the workpiece during machining.
How Does CNC Turning Work?
CNC turning is a methodical and precise process that transforms raw materials into finished products through automated machining. This section will take you through the step-by-step process, highlighting the key features that make CNC turning stand out.
Designing the Part
The process begins with designing the part using Computer-Aided Design (CAD) software. This digital blueprint provides detailed specifications and dimensions for the part to be machined.
Programming the CNC Machine
Once the design is complete, it is converted into a CNC program using Computer-Aided Manufacturing (CAM) software. This program, often written in G-code, directs the CNC machine on how to execute the operations needed to create the part.
Setting Up the Workpiece
The raw material, or workpiece, is securely mounted on the machine’s spindle using a chuck. The machine’s turret is loaded with the appropriate cutting tools required for the job.
Executing the Turning Process
With the program loaded and the workpiece in place, the CNC machine begins the turning process. The spindle rotates the workpiece at high speeds while the cutting tool moves linearly to remove material and shape the part. The machine operates automatically, following the programmed instructions to ensure precision.
Advantages of CNC Turning Over Traditional Methods
CNC turning offers numerous benefits that make it a superior choice compared to traditional turning methods. These advantages include enhanced precision, higher efficiency, consistent quality, design flexibility, and reduced labor costs.
Enhanced Precision and Accuracy
CNC turning delivers exceptional precision, capable of producing parts with tight tolerances. The computer-controlled process ensures every cut is exact, reducing errors significantly. Imagine crafting an aerospace component where even the slightest deviation could result in a catastrophic failure.
Higher Efficiency and Productivity
By automating the turning process, CNC machines can operate continuously with minimal downtime. This automation translates to higher production rates and faster turnaround times. Unlike traditional methods that rely heavily on skilled labor, CNC turning allows for quick adjustments and continuous operation, maximizing productivity.
Consistent Quality and Repeatability
Consistency is a hallmark of CNC turning. Once a program is set, the machine can produce identical parts repeatedly without deviation.
Flexibility in Design and Production
CNC turning offers unparalleled flexibility in design. Complex geometries and intricate designs that are challenging or impossible with traditional methods become achievable. The ability to quickly reprogram machines for different tasks allows manufacturers to adapt to changing demands and custom orders with ease.
Reduced Labor Costs and Manual Intervention
The automation of CNC turning significantly reduces the need for manual intervention. Skilled operators are still essential, but their role shifts from hands-on machining to overseeing the process and making adjustments as needed. This shift leads to lower labor costs and minimizes human error.
Comparison with Traditional Turning Methods
CNC turning offers significant advantages over conventional turning methods. To fully understand these advantages, let’s compare the two methods in a few key areas.
Overview of Traditional Turning Methods
Traditional turning methods involve the manual operation of a lathe and the use of hand tools by a skilled machinist to shape the workpiece. This process requires a high level of expertise and experience to achieve accuracy. While effective for simple tasks, traditional methods are time-consuming and unsuitable for complex, high-precision work. The manual nature of these methods also introduces variability and potential for error in production.
Differences in set-up and operation
Setup of a conventional lathe involves fixing the workpiece, selecting the appropriate cutting tool and manually adjusting the machine settings. Operators must continually monitor and adjust the process to maintain accuracy. In contrast, CNC turning requires initial programming and setup, but once these steps are complete, the machine runs automatically. This automation greatly reduces setup time and the potential for human error.
Quality and Accuracy Comparison
Quality and accuracy are where CNC turning really shines. Traditional turning relies on the skill of the machinist, which can lead to inconsistencies. CNC turning, on the other hand, uses computer programming to control every aspect of the process, ensuring that every part is produced to exact specifications. The high accuracy of CNC machines allows for tighter tolerances and more complex designs that would be difficult to achieve manually.
Efficiency and Productivity Comparison
CNC turning is significantly more efficient and productive. Traditional turning methods are labor and time-intensive and require constant supervision and adjustment. CNC lathe tooling can run continuously with minimal human intervention, greatly increasing productivity. This automation allows manufacturers to complete high-volume production quickly and efficiently, meeting tight deadlines and market demands.
Cost impact and labor requirements
While the initial investment in a CNC machine is higher than that of a conventional lathe, the long-term cost savings are significant. CNC lathes minimize the need for skilled machinists and allow a single operator to oversee multiple machines, thereby reducing labor costs. In addition, the high accuracy of CNC turning reduces material waste and rework costs, which further improves cost-effectiveness. Conventional turning has higher labor costs as each machine requires a skilled operator, resulting in increased expenditure on wages and training.
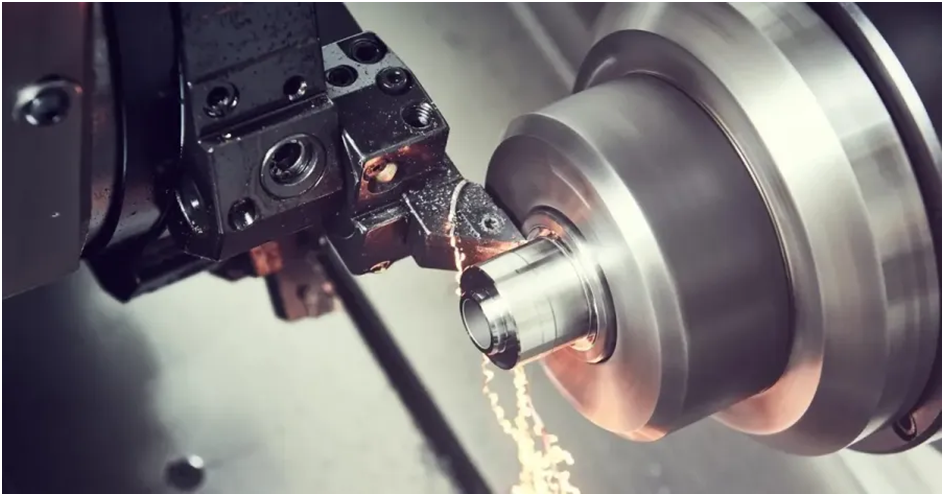
Applications of CNC Turning in Various Industries
Automotive Industry: CNC turning is crucial in the automotive industry for manufacturing engine components, drive shafts, and gear blanks with high precision.
Aerospace Industry: The aerospace industry uses CNC turning to produce turbine blades, landing gear components, and airframe parts that meet strict regulatory standards.
Medical Device Manufacturing: In medical device manufacturing, CNC turning creates surgical instruments, implants, and prosthetics with the necessary precision and repeatability.
Electronics and Telecommunications: CNC turning fabricates intricate connectors, housings, and small components for the electronics and telecommunications industries.
General Manufacturing and Prototyping: General manufacturing and prototyping rely on CNC turning to produce custom parts and prototypes efficiently and accurately.
Conclusion
CNC turning is an automated process of creating precise cylindrical parts, offering high accuracy, efficiency, and flexibility, used in various industries like automotive and aerospace.